IMR Materials Testing Technical Blog
Testing Materials Properties to Mitigate Product Failure in Extreme Operating Environments
A range of high-stakes industries – such as automotive, aerospace, and power generation – require components that function reliably even in extreme temperatures. To ensure these parts can withstand temperature-driven stresses without fracturing, damage, or failure, it’s crucial for manufacturers to subject parts and components to a range of fatigue testing prior to implementation.
By simulating the temperature conditions of a component’s operating environment, fatigue testing enables fabricators to test the materials and designs they plan to use without subjecting personnel or equipment to real-world risks.
Extreme temperature fatigue testing encompasses a range of testing services, both for high-temperature and cold-temperature environments. Determining how temperature stresses will impact intended design functionality helps manufacturers understand the limitations of their components and mitigate the risk of unexpected equipment failure in even the most extreme conditions.
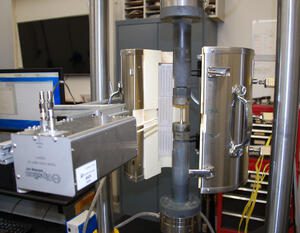
HIGH-TEMPERATURE FATIGUE TESTING
Because of the numerous risks associated with extreme-temperature environments and the potential life or death consequences for equipment operators in the event of component failure, thorough analysis and documentation of high-temperature environment part limitations are incredibly important.
High-temperature fatigue testing subjects manufactured parts to temperatures as high as 1,800° F to assess how predicted mechanical properties withstand the stresses caused at such temperature levels. By examining the thermomechanical and thermodynamic characteristics of materials, fatigue testing enables manufacturers to produce the most durable parts with the longest possible service lives.
Aerospace materials, such as jet engine or rocket components, are key examples of parts that must be subjected to high-temperature fatigue testing; The components need to operate reliably in extremely high operating temperatures while performing a wide range of mechanical functions, such as managing, containing, and expelling heat.
In addition to aerospace components, a wide range of other applications benefit from materials testing and analysis such as ceramics, polymers, metals, glass, and insulators used in:
- Automotive manufacturing
- Furnaces or kilns
- Glass manufacturing
- Military and defense equipment
- Ceramics
- Power generation

CRYOGENIC FATIGUE TESTING
At the opposite end of the extreme temperature spectrum, cryogenic testing simulates extremely cold environments as low as -320° F. This type of testing is specified for any materials that will be used in outer space applications.
Cryogenic fatigue testing involves enclosing a specimen in an insulated fixture attached to a fatigue testing frame, and exposing it to liquid nitrogen to simulate operating temperatures. The analysis will determine how well the test material can tolerate cyclical stresses during prolonged exposure to extreme cold.
Applications that benefit from cryogenic fatigue testing include, but are not limited to:
• RF low-noise amplifiers
• Superconductors
• Electrical components designated for deep-freeze or cryogenic use
• Aerospace (satellites, jet engines, spacecraft)
• Components for nuclear power cooling systems
• Oil & gas valves
• Hydraulics
Cryogenic fatigue testing is suitable for a range of materials used in the above applications, including metals, polymers, composites, and non-metallic/metallic hybrids. These tests can also be performed on finished components.
For more information on IMR’s High-Temperature and Cryogenic Fatigue Testing capabilities, click here.
FATIGUE TESTING AT IMR TEST LABS

A critical step in the manufacturing process, fatigue testing helps manufacturers better understand the capabilities of the products they create before bringing them to market or having them specified into high value, critical-path applications. As such, many OEMs require suppliers to certify their products through an independent, accredited third-party lab.
IMR Test Labs, a global testing firm offering both high-temperature and cryogenic testing, is NADCAP-certified, ISO-certified, and IEC 17025 accredited. We also hold private certifications from major brands in high-performance industries, including Airbus, Boeing, General Electric, and Lockheed Martin.
Utilizing state-of-the-art, in-house equipment, IMR offers a broad range of material testing services to accommodate virtually any field. Our staff of more than 200 professionals – including PhDs, engineers, chemists, metallurgists, and technicians – is available to assist customers with fatigue testing or any of our comprehensive range of testing capabilities. Please visit our fatigue testing page to learn more about our fatigue testing services.
Due to the dangerous temperature ranges, equipment, and chemicals involved, please note that fatigue testing can be extremely hazardous and should only be conducted by trained professionals using proper protective gear and equipment.