THE IMPORTANCE OF FAILURE CAUSE ANALYSIS
Polymers, composites, coatings, or ceramics break down and failure analysis identifies the cause. Failure analysis of materials is important for manufacturers that need to make informed design choices for applications and to avoid costly failures.
FAILURE ANALYSIS METHODS FOR NON-METALLIC MATERIALS
A failure analysis team of chemists, engineers, and lab technicians selects the best testing methods to identify failure conditions based on the visible signs of failure and the material. Failures distinct to different materials require different approaches.
FAILURE ANALYSIS TECHNIQUES
Polymers Failure
Polymers typically fail because the wrong material was chosen for an application or there was an interaction with unexpected chemicals. Polymers fail due to chemical exposure, cracking, or aging.
Composites Failure
Often used in applications of high stress, such as aerospace, fiber reinforced composites fail due to material choice, overestimating the material’s load bearing capacity, or from poor manufacturing practices. Failure is cracks, broken fibers, or delamination.
Coatings Failure
Failures of coatings arise from incompatibility with substrate material or poor adhesion and common causes include delamination, cracking, and erosion.
Metals Failure
Metals typically fail due to material fatigue, corrosion, or excessive stress beyond their design limits. Common failure modes include cracking, fracturing, deformation, or surface degradation caused by environmental exposure and mechanical wear.
Welds Failure
Weld failures often result from poor technique, inadequate materials, or improper preparation. Common causes include cracks, porosity, lack of fusion, or residual stresses, which compromise the weld's structural integrity and durability.
Ceramics Failure
Ceramics are often brittle so thermal stress or environmental exposure leads to failure. Thermal tolerances, fractographic stresses, porosity.
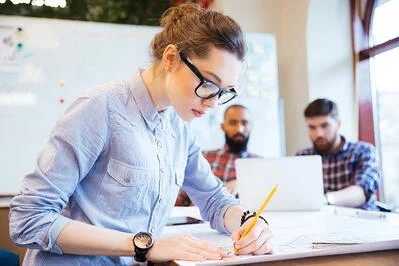
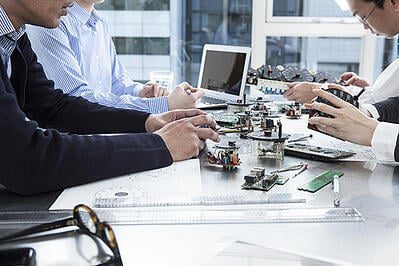
Once signs of failure have been identified, detailed failure analysis can be performed. These tests include:
Physical Testing of Polymers
Physical Testing of Metals
Mechanical Testing
Chemical Analysis
Microscopy
Fractography
Tests replicate the operational environment of the material in order to simulate failures in real-time, providing insight into the failure cause.
EXPERT FAILURE ANALYSIS BY IMR TEST LABS
Specializing in failure analysis for ceramics, coatings, composites, polymers, and other non-metallic materials, the experienced team at IMR Test has the advanced tools necessary to investigate and identify the cause of failure accurately.
It’s not just data, our team provides knowledge: actionable insights to avoid future failures. Recommendations may include modifications or different materials altogether, in order to achieve maximum performance in future applications.
- Expert team of chemists, technicians, and engineers
- Advanced, state-of-the-art analysis and testing equipment
- End-to-end testing cycle and consultation services
Failure Analysis FAQs
IMR Test Labs evaluates a wide range of materials, including metals, polymers, composites, ceramics, and coatings. Our expertise encompasses assessing welds and finished products across various industries.
Our process includes visual examination, non-destructive testing, metallurgical analysis, mechanical testing, and chemical analysis. We employ advanced techniques to thoroughly investigate the failure and provide detailed insights.
The duration of the failure investigation varies based on the complexity of the failure and the specific analyses required. IMR Test Labs strive to deliver timely results with without compromising quality. For a precise timeline, please contact us with the details of your case.
Industries such as aerospace, automotive, energy, medical devices, and manufacturing benefit from our failure analysis services to ensure safety, reliability, and compliance with industry standards.
Yes, beyond identifying root cause, we provide recommendations for design improvements, material selection, and process enhancements to mitigate the risk of future failures. For more information or to discuss your specific needs, please contact us.
LITIGATION FAILURE ANALYSIS
Litigation and insurance claims need support from competent materials testing experts to reach the appropriate conclusions. Our labs in Ithaca, NY and Louisville, KY provide litigation support to clients in a wide range of industries. Clients rely on IMR to provide the following professional services:
- Trial Expert Witness Testimony
- Technical Disposition
- Legal Consultation
- Test Witness Services
FAILURE ANALYSIS TESTING PROCESSES
- Reviewing the steps that occured before the failure
- Simulating the conditions under which the failure occured
- Collecting samples for chemical analysis
- Investigating why some components, if any, remain intact
- Determining the root cause behind the failure
- Recommending steps to avoid future recurrence
In some circumstances, it aids the failure analysis process to inspect the site where the failures took place. Analyzing failures often involves multi-disciplinary processes. These can include the following:
- Chemical analysis through the use of various spectroscopy techniques
- Environmental exposure testing that approximates the operating conditions at the time of the failure's occurence
- Fractography, or the study of the fractured material surfaces
- Microscopic examination using scanning electron microscopes and similar equipment
- Mechanical testing utilizing a wide range of analytical equipment, and taking into account component geometry and failure parameters
FAILURE ANALYSIS TESTING SERVICES
IMR Test Labs offers a comprehensive array of failure analysis services for non-metallic materials, including the following:
- Fractography services, which are particularly useful for determining causes of fractures in plastic components and other non-metallic material surfaces.
- Investigative chemistry, including adhesive identification, coating contamination, contaminant identification, paint identification, and surface contamination. These are useful for analyzing paint adhesion failures and determining the presence of contaminants in paints and plastics.
- Physical testing for benchmarking plastic part materials and determining distribution of fibers in fiber-reinforced plastics, among others.
- Residual analysis, such as FTIR, scanning electron microscopy and energy dispersive X-ray analysis (there is a close relationship between investigative chemistry and residual analysis) for contaminant identification.
- Thermal analysis for measuring properties such as melting point, crystallization temperature, filler content and mechanical properties as a function of temperature.
- Litigation failure analysis, involving trial expert witness testimony, technical disposition, legal consultation, and test witness services.
The above services are available for a wide range of materials and parts, including electrical components, fabrics, medical tools and devices, plated parts, plastics, and printed circuit boards.
POLYMER / COMPOSITE FAILURE ANALYSIS SERVICES
Failure analysis of non-metallic materials is necessary to prevent the future recurrence of failures in non-metallic materials. There are different kinds of non-metallic failure analysis techniques. The use of these techniques ultimately depends on the type of non-metallic material to be analyzed and tested.
Request a quote to know more about our non-metallic failure analysis services.
Paints & Coatings
Coating Shear Fatigue
Coating Thickness
Dime Scrape
Flexibility
Impact Resistance
Material Identification (Base Polymer)
Material Properties of Liquid Paints and Coatings
MIL-STD-801 Section 504 Testing (Contamination by Fluids)
Pencil Hardness
Solvent Resistance
Specular Glass (20° and 60°)
Stain Resistance
Failure Analysis
Failure Mechanism
Root Cause
Applied Stresses
Fracture Origin
Trace Contaminants
Material Characterization
Additive Analysis to Trace Level
Bond Strength
Chemical Exposure Testing
Coefficient of Friction
Compression Set
Compressive Properties (-40°F to 660°F)
Density & Specific Gravity
DSC Analysis: Melting Point Glass Transition % Crystallinity
Dynamic Mechanical Analyzer (DMA) Testing
Extractables
Fatigue Testing (ambient temperature)
Flammability
Flexural Properties (-40°F to 660°F)
FTIR Analysis
Hardness (Rockwell, Durometer, Barcol)
Trace Analysis
Polymer Additives
Plasticizers
Leachable Compounds
Extractable Compounds
Semi-Volatile Compounds
Contaminants
Corrodents
XRD Analysis
Identification of Unkown Powders
Analysis of Corrosion Products
Phase Identification
Crystal Structure
Reverse Engineering
Competitive Analysis
Material Confirmation
Material Characterization
Hardness (Rockwell, Durometer, Barcol)
Heat Aging
Impact Strength
Lap Shear Testing
Material Identification
Melt Flow Rate/Index
SEM/EDS Analysis: Fillers
Tensile Properties (-40°F to 660°F)
TGA Analysis: Polymer Glass and Ash Content
TMA: Glass Transition, Coefficient of Thermal Expansion, Heat Deflection Viscosity
RELEVANT ACCREDITATIONS
Click here for our full list of accreditations and certifications